Unisteel’s experience working with the high-strength materials used in wire forming enables the production of miniature springs and multi-component assemblies that marry wire forming with different technologies.
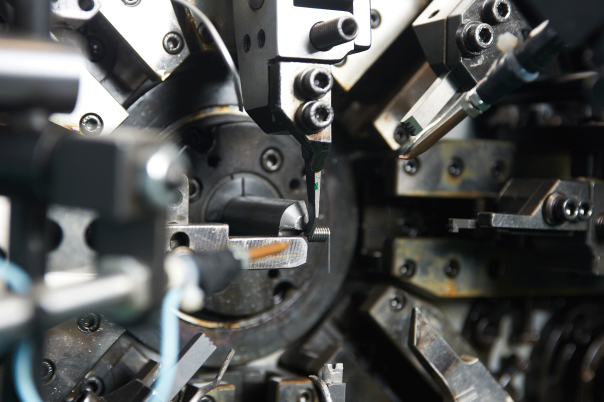
Unisteel’s experience working with the high-strength materials used in wire forming enables the production of miniature springs and multi-component assemblies that marry wire forming with different technologies.
The tiny springs for smart wearables
Wire forming products are a crucial component commonly used in electronics, especially as demand for compact devices grows. From as small as 0.08mm in wire diameter, Unisteel works with both ferrous and non-ferrous materials to create the micro wire forms found in smart wearables and products with an ultra-slim profile.
Multi-component assemblies – the best of both worlds
In-mold riveting is a special technique to optimize assembly of multiple components. This revolutionary technology makes it possible to integrate wire forming and precision stamping. Unlike the traditional method, where assembly takes place in a separate process after the components have been produced, Unisteel’s in-mold riveting technology enables assembly to be designed into the production of the main components. This means multiple processes can be completed in a single stage. The process is fully automated, providing increased repeatability and productivity and reducing defects due to handling error.
Working with high-strength materials
Unisteel's wire forms can be manufactured with materials of high strength and hardness, such as SUS301SH. A high-frequency heater is introduced before the wire forming process to heat up the material prior to forming. This allows it to be formed beyond its limits without any of the fractures usually found in high-strength materials.
Inventing success together
We offer customized manufacturing solutions with added-value to our customers and are deeply involved in every stage of product development – from design to prototyping to mass production. Our engineers work closely with customers to ensure every product manufactured conforms to design and is precisely engineered.